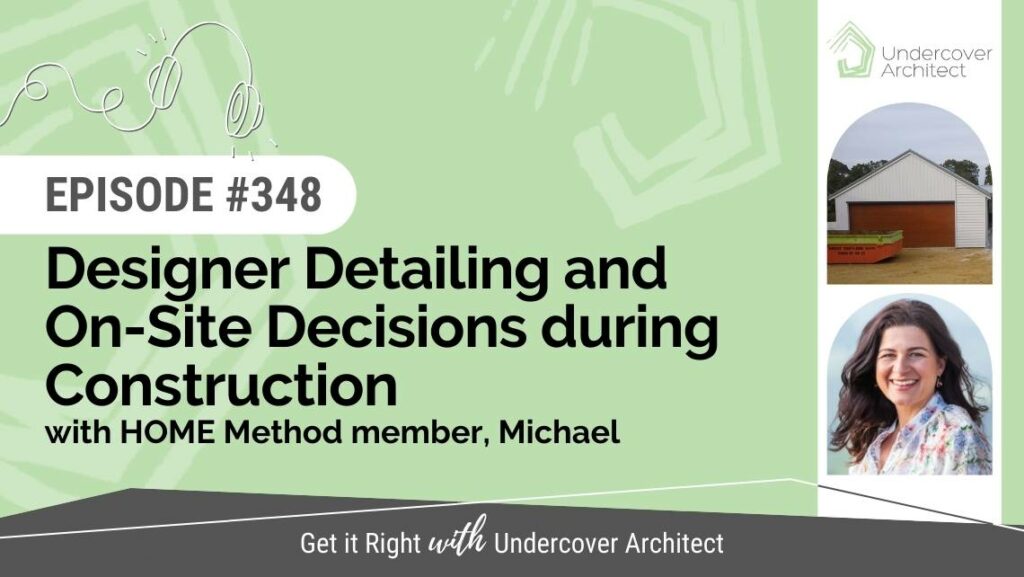
How do you get it right with designer detailing so you can manage on-site decisions during construction?
How much needs to be decided and drawn? And what can be left for the construction stage?
Michael gives us the latest update on his new build in West Australia.
You’ll hear more about what that’s meant for his role on his project, and the process of working with his designer and builder during construction.
Listen to the episode now.
Hello! This is Episode 348, and I’m back with HOME Method member, Michael as we continue the conversation about the construction of his new home in Western Australia – a home that he and his wife intend to retire to and enjoy a relaxing lifestyle that makes the most of the beautiful location.
If you missed Part 1 of this conversation, head back to Episode 347 to listen first before diving into this one, as it’ll make a lot more sense if you do. Head to Episode 347 here.
Michael was on the podcast earlier in our HOME Method member stories, in Episode 323 and Episode 324, discussing the earlier parts of his project. So it’s great to have him back with this construction update.
We finished the last episode with Michael sharing info on his home’s energy efficiency assessment and the changes they made to improve the home’s star rating.
As a reminder: West Australia at the time of recording this episode, decided to not bring any of the NCC2022 changes into their building codes until 2025. So, the decade-old 6 star energy rating is still the requirement there.
I kick off Part 2 by asking Michael how he believes this home will perform compared to where they are now.
We talk about the gaps that Michael has needed to bridge between the documentation and the construction on site, with some changes based on on-site design decisions, material changes and detailing consequences.
We also talk about the roles that both he and his wife have taken on in this project, especially as Michael initially had assumed he wouldn’t be too involved.
And Michael also shares how the construction process has gone, how frequently he’s been on site given it’s 120km away from where they live, and how the interior is feeling now it’s at a point you can perceive volume and space.
LISTEN TO THE EPISODE NOW.
I also want to draw your attention to the conversations we have about detailing changes and decisions on site, and share a few things to be aware of before we dive into this conversation.
In the last episode, Michael discussed some of the challenges that come when changes are being made on site, and we discuss more here as well.
Michael is talking about a lot of the real life scenarios that can happen when …
- You don’t use a collaborative pre-construction process such as the PAC Process where the builder is involved in the design phase of the project, so they don’t have intimate familiarity with the details of the project often until they’re on site, figuring out how to build them.
- The designer is not closely involved in the construction process, so you, as the client and Project Manager, are navigating proposed changes from the builder during construction, and then having to resolve their impact on the design overall, and then the builder is executing without updated drawings.
- The designer does not sufficiently resolve some of the detailing and selections in their dealings with you and their documentation, prior to them wrapping up their services with you.
- You change things on site: either out of necessity because they weren’t effectively resolved and documented during design, or because the builder suggests something they feel will be better, or you change your mind about something now you see it being constructed.
Listen to this conversation because you’ll hear how changes have been navigated, and then what that’s meant for Michael’s involvement and decision-making process.
Before we jump in, here’s some timing for context on my conversation with Michael.
Michael joined HOME Method in April 2021. We recorded this conversation in mid-May 2024. Site works began on Michael’s project in January 2024, and it’s due for completion in 2025.
Let’s jump into my conversation with Michael now.
This is the transcript of my conversation with Michael discussing his role in his project, and managing on-site changes during construction.
Amelia Lee
What’s your house like that you live in at the moment? Is this going to be a big jump up in terms of its comfort and its performance overall?
Michael
Definitely. The home on the farm, I suppose, it’s a bit like yours. It’s an old jar of framed home with no insulation. It’s got plaster on the walls and it had asbestos linings on the outside. We renovated in 2020, I think it was, 2022, it would have been, and we clad the outside. We insulated the ceiling so there’s still no insulation in the walls, but the double wall cladding has helped. I just remember, we’ve got verandahs around the north side. We reused a lot of the jar that was in the shed that used to be a part of our house. And then, I just remember, when the iron went on the rounder and all the light disappeared out of the house, I just thought, “Well, just miss that light, but it’s good in summer because it gives us some shading.”
But yeah, definitely, I know the fires cranking in the evenings, and so, look forward to have a nice home that’s comfortable to live in, that doesn’t need a lot of that heating and cooling. We’ve designed it with cross ventilation and that sort of thing. So, in the summer, if it’s a bit warm, we just crack a window or whatever.
Amelia Lee
Yeah, I think it’s going to be a big step up for you. It’ll be absolutely amazing to see how much more comfortable it is for you. You mentioned that you’ve had a dry period since you started construction, obviously. So construction has moved ahead.
Can you talk through how construction has been for you, in terms of how regularly you’ve visited site, the kinds of conversations that you’ve been having with the builder, and if there’s been any surprises along the way in terms of how that’s been rolling out?
Michael
No major surprises, but a few challenges, I suppose you would say. The aim was to get the site works and the pad down before Christmas, but that didn’t happen. We might have got site work started, but the builder didn’t want to leave exposed sand pad. We had, I’m trying to think of the gradient, it’s about a 1 to 10 gradient, something like that. So, there’s quite a lot of fill that went in. So, we didn’t do a cut and fill. We just mostly did fill. So that was a week’s worth of trucking in and leveling and that sort of thing.
So basically, mid January, they started on that. And then the progression was went really smoothly. And we were very pleased with the standard and the finish that they were doing. They got a contractor with a big loader in and he just scalped all the surface and pushed some banks down the hill. And the guys just did a fantastic job and everything ran along very well. I think the relationship with the builder and his own trades, and then the trades that he employs has been very positive. So, yeah, everything progressed well along those lines. And communication with the builder is very much ‘Let’s deal with what’s in front of us.’ And one thing that my wife and I would have liked to have done, and we thought was going to happen, was actually sit down and go through the project. “These are the steps, and I think there might be some issues here.” We didn’t get that opportunity. So, it’s probably had a couple of challenges, and then suddenly you’re dealing with that.
You’ll get a phone call and say, “This is an issue.” And I know one of the first issues was around the fireplace and fire selection, and actually just kept trying to get specifications. Being a brick fireplace, it was really hard to get specifications for a non combustible surface, like brick. So that was challenging. We ended up, we started talking to a local fire and store, and he came out on site, and then went away and I learned that the first fire we selected, so it’s an insert type wood fire, and so we went away from that. And we went to another brand. And then, we weren’t getting much information out of our local supplier, so I actually went directly to the importer to get information. And suddenly the hearth on the fire was going to be 600 mils into the room, and we’ve got a timber floor. And we thought, “Wow, this is actually going to be impactful on the looks.” And so we had some conversations on site and how’s this all going to go? And builders obviously got to tell the bricky how this is all going to come together and how you’re going to manage it all. And then he left, and then he flipped me another supplier, and he said, “How about you try this mob?” So then we rang them, and we found out, well, they actually do all their own testing of their fires in an enclosed area. So then, the specifications gave us a lot more options as to how it was actually installed.
So, the builder was getting bit frustrated, and I think he spent a couple of days trying to get information, and so, yeah, that was a bit of a challenge. But we ended up getting that all sorted. But it does take some phone calls and eventually finding people that can give you the answers. And, yeah, that was a bit of a challenge. And, I think, if we’re doing it again, we might not have had an insert fire into a fireplace. We might have had the free standing fire with the flue, and designed it differently if we had known that challenge was there early on in the build. In the design phase, we might have designed it differently. We certainly could have changed that.
Amelia Lee
Is that because this is how the builder works, like, you said you wish you’d had the opportunity to sit down with them and go through and identify the things? Because the conversation that you had before about the designer and their level of involvement, is there a lot that’s happened because it’s not been necessarily documented or figured out by the designer in terms of the actual specification of the product, so then the builder looks at it, and then it comes back to you saying, “Well, hey, we’ve got these problems.” And then you start doing your research and nutting it out. Do you think that there would have been a different way that you would have liked to have seen those relationships work in terms of how it could have flowed a bit more simply for you?
Michael
Yeah, certainly. From the builder’s point of view, he’s saying, “Well, did the designer even talk to you about this?” And we said, “Well, no, he just designed it.” And he actually had down pipes inside the fireplace. And obviously, that would have to be inside a double brick cavity. Otherwise, you’ve got all that heat inside there. So there’s different practical design issues that we came up against.
And then, that specifying, there was no conversations. And that’s something that we probably didn’t understand, where does the designer stop and where does the builder start? And I think that’s that little bit of gray area in between that definitely, if the builder and the designer in the same room, all those sort of challenges are solved. And we used an interior designer a little bit late in the process, but it actually brought up a couple of little challenges – not challenges – she just picked up a couple of things like maybe that room should be bigger, certainly in our mud room area, we redesigned that, and a little bit around the study. But she did say, “Well, these are high level. I don’t normally see design drawings at this level.” And then, the builder’s saying, “There should be more detail in this.”
And maybe some of that’s also… Our design did evolve a bit. And so there was that 12 months where we had the base design. So, come back to the designer after a pause of a few months, and so then it’s picking it back up. And then, yeah, we flipped a couple of things right at the end. And I know there’s a couple of things on the drawings… He uses a drafty to finalise the drawings. And there’s certainly some measurements where we changed their en suite, and things that weren’t on the drawings. They weren’t major issues, but, yeah, I think it was just that little bit of detail and that little bit of time just to make sure.
But overall, I think the design drawings were adequate for a builder to build from.
Amelia Lee
And how have you found, in terms of the role that you’ve played in construction process, because it sounds to me like you’ve continued that role of we dive into the nuts and bolts and help figuring out what is the best way to go about getting the esthetic outcome that we want that’s also going to satisfy functionality, construction, those kinds of things. Have you found that that’s been more demanding of your time? Or have you been happy with how that rolled out? It’s only just been a few of these kinds of, I suppose, particular challenges that have come up here and there.
Michael
Trying to work out how often we’d go in, I mean, we probably try to get in there close to once a week, but maybe once every 10 days, I guess. Because we’re 120 kilometres from our build site, and we try to line it up. So we were in there on the weekend, and obviously the builder wasn’t there. But we just did a bit around the site.
But I haven’t found it too demanding. I think, probably the fireplace was the most challenging thing. We did get a phone call from the builder, and my wife was actually in Melbourne with my two daughters at the time, and it was a bit around the alignment of the gutters. And so we’ve got 30 degree pitch on the two pavilions. And then I’m not sure what it is, probably might be 12 degrees, or it’s a fairly low pitch on the connecting area. And then we’ve got a feature brick wall just on the entrance. So that we’ve got about a metre where the gutter, then, of course, double brick is wider than a stud frame wall. So that’s an area that, I think, initially, the builders were going to run the gutter around the brick, and then I think they decided to bring the gutters out in line with the brick wall. So that meant then a decision of, do we have some eaves rather than being right flush to the wall? And the different pitch on the connecting area meant the eaves were probably 600 mil, and then we had just very small eaves on the rest to just get it all aligned. And there’s probably something we didn’t take it to the designer, because I think he would have disagreed with it. But I think we’re quite happy. I’m quite happy to actually have some eaves. I don’t think there’s plenty of our buildings like our design that have eaves on them, so I think it’s worked out fine.
And my most important thing, the builder was saying, “How do I get the right fall on the gutters and different things?” So there’s a lot of that practical side of the detail. And I talked to my wife about it, we were happy to go with his best advice on that. So, yeah, I think we’re not going to be disappointed with it, put it that way.
Amelia Lee
How have you found the roles between you and your partner have changed from what you first anticipated? Because you said at the beginning you weren’t engaged, and then you started diving in down the rabbit hole, you found Undercover Architect, you joined HOME Method, you’re the one that’s inside HOME Method that I know is part of the community and asking questions on a regular basis, and sharing your progress as well. How have you found that your roles have played out in the project, and has that been unexpected for you, or has that generally worked?
Michael
I certainly try to get my wife engaged in Undercover Architect, and I got her to listen to your, I think, it was podcast 200, which I thought was a fantastic insight into yourself and why you do it. And she’s listened to a few. So, I always tell her what’s happening, and I think we had the design review. I mean, she’s watched that, and there’s certainly been engagement. But I’ve really enjoyed the structure and the design and how it all comes together as a build. And there’s been push back from the builder, because the cabinet makers really busy at the moment, but we haven’t finalised the kitchen design and the cabinetry. So there are areas that she’s really engaged in. She knows the styles that she wants, the finishes we want. I want to have a timber island bench top, I’ve got some timber there. And she says, “Oh no, but it won’t be durable.” And well, I say, “Well, it depends on the finishes, and how you do it.”
So there’ll be a few little challenges like that, but it’s all doable. And I loved your little laugh the other day about the kitchen design and the position of the fridge, because I know that if I’m under her feet…
There’s areas that got to be designed well, so you can operate them. So that’s an area that we’ll get to. But she loves her cooking and that sort of thing, so it’s not something I want to dominate, but just want to make sure that it does work well.
Amelia Lee
Yeah, you came to the group with questions about the layout and the fridge location, and whether that was worth having out from the kitchen at 90 degrees to it, or whether brought it in alignment with the back joinery. So yeah, it was funny to give you that feedback, but then say, “Just leave it where it was designed in the first place, because it works best there.” So, it’s one of those tricky things, isn’t it? But, I mean, that’s the thing. In all of my dealings with you, it’s been very clear that you are really thinking through with a lot of intention. Not just mentally rehearsing what this home is going to be like to live in, how you’re going to share it with your family, what it’s going to be like when it’s just the two of you there on your own, how it’s going to work for you, but you’ve also been super intentional about the level of research and understanding that you’ve sought to achieve for the materials and the detailing and the construction methodology.
So, it’s always a joy to have you pop into the community and share where you’re up to, and then share your questions. Because I know that they come from a place of you really wanting to create the best possible outcome for the budget and the site and the home that you’ve been envisaging all this time.
Michael
Look, it’s been fun. I’m trying to think, the lady south of Adelaide, those two podcasts were absolutely fantastic.
Amelia Lee
Oh, Clare?
Michael
Yeah, Clare, that’s right. Actually, I was in Adelaide just prior too. I would have loved to have gone down and had a look at the home. She did reach out. She did say, “Yeah, no problems.” But yeah, I just think what she’s done is just amazing, to end up with a result and achieve the goals, and her selection of builder and the way they work together, it just sounds fantastic.
Amelia Lee
I think it’s really exciting. She’s now working with her builder more closely and assisting him in his other projects. What I love seeing about HOME Method is that ripple effect that you upskilling yourselves in this way, I mean you will have had an impact on your builder in terms of how they’ll have made decisions, and the things that you will have uncovered and the research to impact how your project gets built will have a ripple effect on the way that they do other people’s projects in the future. And the same for Clare working more closely with her builder now and opening her home for Sustainable House Day to demonstrate to people what it’s like. And I got lots of messages from people saying that it was just so lovely to be in a home that showed what was possible, and that you could achieve.
I think people think that sustainability has to look a certain way, and a healthy home has to look a certain way, but it comes in so many different packages because it’s so driven by what your own priorities are. It’s really great when people start disrupting those conventional status quo ideals that we have about it. So yeah, it’s great that you enjoyed the episode. And I’m sure that if you reached out to Clare, being in the community, and you’re in Adelaide again, I’m sure she’d be happy to give you a look around. So now, I’m very conscious of your time, because I know you’re a very busy man. I just wanted to see, with the construction process, where are you at now? Like, where are you at progress-wise for what’s been done on site?
Michael
So, the roof is on, the gutters are on. So yeah, it’ll be wall cladding next. So, the builder, the end of this week, he’s having 10 days off, I think. So yeah, I think there’ll be just a little pause, and then they’ll be back into it. There’s one interesting thing we’ve done is we’re actually going to put a concrete water tank in, because we’ve had some interesting conversations. One of the first things the builder said to us, “You’ll need to have good filtration.” And we said,” Well, we’re going to have rainwater tanks.” And he did say, “Well, the water’s acid, so you’ll need to, I’m trying to think what you call it, but anyway…”
Amelia Lee
love house filter before it comes back into your taps?
Michael
Yeah. But then I said to him, because we’re going to have retaining walls, because we’re dropping the tanks in, we’re going to have concrete retaining walls. And then, some of the actually relevant is they’re not far away, and we know the people actually have Denmark Concrete. And we talked about concrete tanks, because concrete tanks always used to be a little bit alkaline. And then he said, “Oh yeah, Brandon, he’s just starting to do concrete tanks.”
Because in some of the fire-prone areas, they’re finding that your water security is compromised in poly tanks or steel plastic-lined tanks. So there’s a little bit of a move back to concrete, and the systems are quite different. Now, they’ve got polymers in them. And it’s not just steel mesh and that sort of thing. And there used to be trouble with cracking and that sort of thing. So they’re building a couple down at Denmark. And so they’re their prototypes and then they’re going to do ours, and that’s an interesting thing. City of Albany is demanding engineering, and Denmark’s not. So, that’s an interesting space.
But the concrete tank will also double as retaining walls, so we get a double win.
Amelia Lee
That’s a great strategy.
Michael
Yeah. So, that’s an area that I think conversation developed, and I think we’ll get a good outcome with that.
Amelia Lee
How big are the tanks going to be?
Michael
It’s the old 12,000 gallons, which is, I think, 43,000 liters, or no, it must be more than that. Anyway, around in that lad. I think we had to, whatever 12 is by 4.5, so it won’t have the capacity of the two tanks that we had. We had 2 38,000, give you 76,000 liters. So I think it must be something like 60,000 liters or something. So that’s where we’ve landed with that.
Amelia Lee
Do you need one dedicated for firefighting as part of the fire solution on site? Or are you able to use them and have them for firefighting as well?
Michael
Certainly, we’re going to keep access and have an outlet for firefighting, and that’s something we’ve always wanted to have water on. I don’t think it was a stipulation by the City of Albany for firefighting, but it is something that we will have this reasonable amount of forest not too far away. We’re a BAL 19, and it goes to a BAL 29 not too far from our site, and then to a 40 and then to flame zone on the edge of our one hectare block. So we’re quite well away from the trees, but it is an area that you never know with. It’s quite forested on the river verge and that sort of thing.
Amelia Lee
And tell me, now that you’ve got the roof on and the wrap, have you been out to see the project and how to wander around inside now the volume feels contained?
Michael
Yes, and I think we’ve got where our bathroom is. It’s at the southern end. So it’s not the ensuite, but the bathroom to the other two bedrooms. And then we’ve got a back to wall bath, and then there’s a window above it. So we’ve held off about the seal height. And the window there and the window outside, just the entry, they both look west into the alcove between, and that’s the entrance area between the two pavilions. So we’re actually going to lift the head height of the windows up just to get a bit more afternoon sun. And that’s something that, when the roof’s on, you’re basically looking straight in just below the ridge line through the head height at 2100. But when we go to 2400, we’ll actually get that view directly out over the ridge line to the sky and a bit of extra afternoon sun. And then it’ll align with the second living space that’s got a 2400 head on the windows. So, yeah, that’s just one of the few changes we’ve made with the windows.
I think, when the wall frames went up, we narrowed up the two bedroom windows by a couple 100 mils. So they went from 2200 down to 2 metres wide. So that’s another change.
Amelia Lee
How are the spaces feeling?
Michael
We’re very happy with the spaces. Actually, one thing, walking down, just for privacy for the two spare bedrooms and the bathroom, we put a cavity slider in there. And one of the builders, it’s his idea… The cavity slider, because the pantry cabinet or something, that’s 600 deep, and then the cavity slider, it was still intruding into the open way, so he said, “Well, why don’t you make this slider so you have that full open hallway, or area?” So yeah, so there’s a couple little things like that that have changed that just make it flow better, so you can still close it for privacy, or it opens up and it just looks like it’s not there.
Amelia Lee
I’m just wondering, if you can share with me, what are you most looking forward to when you move into the finished home? Like, you’re probably still a fair few months away, but it’s been a long journey for you. So, what are you most looking forward to?
Michael
It’s a beautiful spot, and the birds, and there was a lot of blue wrens and that sort of thing, so it’s nice and quiet. We’ve got lovely neighbors next door. But maybe getting the kayak and jumping on the water and, yeah, just have a bit of relaxing time, and just enjoying that little bit of transition from working hard on the farm. And, I think, the trouble is, being on the farm is, when you’re there, there’s always work. Whereas if you get away… And, I mean, the workshops at the bottom end, we’re going to wait, make sure the house is through the process, and then we’ve got a pad sitting there with a bit of plumbing at the moment, we’ll get the pad down at some point. And then, I’m looking forward to getting the workshop up and going, and getting some of my woodworking timber in there and just enjoying a bit of that sort of thing, couple of hobbies. And so yeah, I’m looking forward to it.
Amelia Lee
And did you have anything else to share before we wrap up about the construction process or anything that, to date, with where you’re at in your project?
Michael
Just enjoying the construction process. I’m really enjoying. The trades are great. And my wife took down some muffins the other morning when she went down there. And, I think, they were working on the roofing at the time. And yeah, they’re great people. And just really enjoying that process and seeing it all come together. And we bought the block, and it was like, we had a nice northern aspect and outlook, and what design are we going to be here? We wanted to work out how to get the best out of the site and utilise solar passive design, and now we’ve got something we think works really well.
Amelia Lee
Yeah, I’m so excited for you to both move in there and get to enjoy it after all of your hard work of making it a reality. So, thank you so much, Michael for updating us on where you’re at. And yeah, can’t wait to see what’s ahead, and have another chat to you when you’ve moved in, and you can let us know what it’s like to actually live in as a home.
Michael
Thanks, Amelia. I really appreciate the conversation, and I’ve really enjoyed being engaged in Undercover Architect. I think it’s just a fantastic resource.
Amelia Lee
Thank you.
One thing to be aware of in a custom project is that a lot of detailed decisions get made in how your finished home is built.
Many of these can be made during the design phase. You can catch a lot of them, but it can be hard to catch ALL of them – purely because it’s a custom build, and the first time this project is being built ever. However, an experienced designer, especially working inside a collaborative pre-construction process that involves a builder as well, such as the PAC Process, will be able to iron out a lot of the details, and understand what needs to be documented to assist accurate delivery on site.
Some decisions will, however, need to be made on site. And, if you change anything on site during the build that deviates from the design drawings, then that will have an on flow effect on detailing and construction decisions overall, possibly beyond the specific change you were making.
So, if your designer isn’t involved in construction, and your builder isn’t involved in design, it’ll mean you, as the homeowner and client, will need to Project Manage this.
And if you care about what it will look like or how it will function, you’ll need to get involved and work to understand what’s going on – especially so you can yay or nay any proposed changes confidently.
This is where a lot of homeowners get unstuck.
A builder will suggest a change for a range of reasons. You will approve the change they’re proposing, not necessarily understanding what it’ll look like, or the impact it may have on other parts of your home’s look and functionality.
The builder is not a designer, and they may not understand until after the ball is rolling on the change what the flow on effect will be. And you can end up with something you didn’t intend to have or want – but weren’t able to visualise it sufficiently to catch it before it all happened.
In Michael’s case, there were obviously things that didn’t get fully nutted out with the designer … which can be
- an experience thing (as in the designer doesn’t have sufficient experience to know all the assumptions to iron out)
- a fee or scope of works thing (as in the designer wasn’t commissioned to do that level of detail resolution)
- or a timing thing (as in construction isn’t beginning for some time, and the client wants to delay certain decisions for a range of reasons).
And then the builder has also suggested changes on site, which have necessitated design and detail decisions to resolve.
You also heard Michael say that they’d assumed the builder would sit down and go through everything with them regarding detailing etc – and the builder didn’t. I’d assume because the builder is used to working off drawings and then making a bunch of decisions on site.
And even though Michael lives 120km away from the site, it’s clear that he’s been able to stay ahead of construction, and also communicate openly with the builder about these changes so that they can be resolved satisfactorily.
This is the thing: You can build a home from 5 drawings as much as you can build a home from 500 drawings – but one of those options will have the builder making a lot more decisions on site because the information isn’t drawn.
I encourage you to think about what your expectations are for how this will go in your project.
Think about:
- How involved do you want to be in all the detail decisions in your project?
- Do you want your builder to be really familiar with the design, and even be helping out with those detail decisions, whilst the project is still in design?
- Do you plan to be visiting site regularly to answer questions and review work proactively?
- Are you expecting your builder to discuss things in detail with you, or check in with you before making calls on things that aren’t in your drawings?
- Do you care if details get changed during construction from what you’ve done with your designer, especially if they’re cheaper or faster to build?
- Will you take issue with your builder making suggested changes, or do you just want them to stick to the drawings?
- Are you expecting you’ll be able to make changes during construction, or delay certain decisions until then?
- What are you willing to pay for in pre-construction services from your designer and builder, and how will that impact what work needs to be done by you in your project?
Think about these questions, and also discuss them with your team. I think it’ll open up some great conversations and, most probably, highlight some assumptions you’re making about your project.
RESOURCES
Check out Michael’s previous episodes on the podcast here:
- Episode 323 ‘Building a New Home for Retirement, with Michael’ >>> https://undercoverarchitect.com/podcast-building-a-new-home-for-retirement/
- Episode 324 ‘Volume Builder vs Custom Builder for a New Home Build, with Michael’ >>> https://undercoverarchitect.com/podcast-volume-builder-vs-custom-builder-new-home-build/
- Episode 347 ‘Choosing the Best Builder with Budget in Mind, with Michael’ >>> https://undercoverarchitect.com/podcast-choosing-best-builder-with-budget/
Sustainable Builders Yak podcast on Spotify >>> https://open.spotify.com/show/6Ab8lzXkoAKC5qXMG3qHHl?si=1ac076ba0ef64c9a
Check out Clare’s previous episodes on the podcast here:
- Episode 313 ‘Building a Sustainable New Home: Here’s How to Get It Right’ >>> https://undercoverarchitect.com/podcast-building-a-sustainable-new-home/
- Episode 314 ‘Design a Home for How You Want to Feel in It Everyday’ >>> https://undercoverarchitect.com/podcast-design-a-home-for-how-you-want-to-feel/
Access the support and guidance you need (like Michael did) to be confident and empowered when renovating and building your family home inside my flagship online program, HOME METHOD >>> https://undercoverarchitect.com/courses/the-home-method/
Learn more about how to interview and select the right builder with the Choose Your Builder mini-course >>> https://undercoverarchitect.com/courses/choose-your-builder
Access my free online workshop “Your Project Plan” >>> https://undercoverarchitect.com/projectplan
Leave a Reply