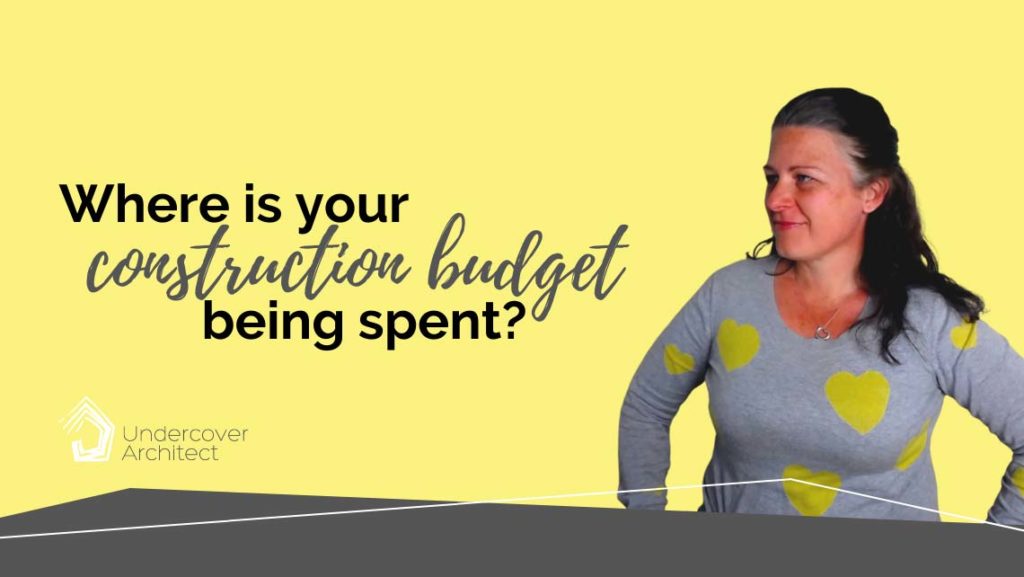
Where is your construction budget being spent in your renovation or new build?
And are you focussing your money saving efforts in the right place? Learn more here.
When it comes to the cost of your build, (whether renovating or building new), you’ll most likely find that it’s 50/50 …
50% materials and 50% labour.
(With the current price rises that have been occurring, which have been coming through at a rapid pace, this may have shifted a little. However, this is a statistic that has rung true for quite some time).
This may come as a surprise to you. However it’s worth thinking about, so you can focus your money saving efforts in the places it’ll have the most impact.
Many homeowners expend a lot of effort and time to whittle down their selections.
They work very hard to save $$ here and there on their lighting, tiling, joinery, windows and all the other material and product choices.
And that is understandable. Your finishes and fixtures are tangible things. You can see them, make enquiries about them, see price points online, and figure out the cost of them based on how much or how many you want to include in your future home.
So it can feel accessible to take control of your construction budget in these areas, and try to manage your costs yourself.
When I was part of the Senior Design Team at Mirvac Queensland, at the outset of a project we would be briefed with a budget for all the interior fixtures and finishes.
Working closely with the Construction and Estimating department, the Development Manager (who managed the project’s budget and determined its feasibility, much like you do as a client), would determine the benchmark of the project and what that meant for the finishes and fixtures budget.
Based on the market they wanted to target the project to, and the kind of sale prices they were hoping to get, and benchmarked against other similar projects both in Mirvac and in the marketplace, that would drive the standard and type of finishes we (as the Design team) were briefed on.
Right from the outset, the Development team would have a target construction budget plugged into their feasibility. And the Construction team would determine whether this construction budget was achievable based on the site and the intended style of construction.
Plugged into that budget were allowances for all the fixtures and finishes, aligned with the standard of finishes briefed by the Development team.
So we, as the Design team – and more specifically, the Interior Designer, would get told … “you have (say) $40/m2 for floor tiles, and we’ve allowed laying costs for a 600x600mm” and “you have ‘x’ amount for each of the bathroom fixtures”, and this went on for every single interior finish and fixture in the project. Door handles, carpet, tapware, light fittings. Everything.
And then we, as a Design team, would move along the design phase, juggling that budget.
The Interior Designer would inevitably find an incredible tap they liked that was over the budget, so then they’d find a lower cost toilet to pay for the difference. Perhaps a more expensive tile was found, but it was only going to be a feature tile, so a more budget option was chosen for the main tile, to offset the cost overall.
This would go on for AGES. And, when you’re doing hundreds of apartments or houses at a time, it makes sense to do this. A $5 saving on a tile over that many square metres can make a big difference to the overall cost of the project.
Borrowing from Peter to pay Paul. Wheeling and dealing to scrimp and save where we could.
One day, my boss said “Enough! We spend months and months, and so many meetings, discussing $5/m2 on a tile. Let’s look at how much of the TOTAL construction budget these finishes actually account for, and if we’re focussing our efforts in the best place.”
Interestingly, they only contributed for around 15% of the total construction budget.
So, we started looking for (chunkier and bigger) ways we could change the design to save money in other areas that had a greater impact.
Time is money when it comes to construction, and in Australia and New Zealand especially, labour costs are quite high.
So where could we reduce the labour requirements in the projects? Where could we make something simpler to build? Where could things be built faster, with less labour, and be more efficient overall?
Of course, these are big projects, so it makes sense.
However, the same also applies to your individual renovation or new build.
Many homeowners will totally hone in on their finishes and fixtures and juggle their budget, seeing where they can scrimp and save to reduce their project costs.
However, they don’t look at where their project could be more simply built, or built faster, and big savings made in labour costs.
So, how can you do this?
(I mean, if you don’t build houses yourself, it can be challenging to figure out how to build simpler and faster, can’t it?!)
Getting a builder involved early in your project (during the design phase) can assist with identifying ways your intended design can be streamlined and built more efficiently.
A builder can work collaboratively with your designer or architect to be strategising about this as the design develops.
Using the PAC Process in your project, and working closely with your designer and builder, you’ll also be able to identify budget amounts for your fixtures and finishes early on. This will give you helpful constraints to work to, so you’re not aimlessly choosing your finishes and fixtures.
Or if there’s a specific thing you do want, you can see how it will inform your overall construction budget in real time.
Plus, when a builder and designer is working together, they will be able to identify opportunities to streamline structural design, speed of construction, and the amount of labour required, and improve the design where needed.
As the design is being developed – not after it’s finished.
If you’re not using the PAC Process, then work out how you’ll build this into your design phase with other costing professionals and building experts, to help inform your design journey.
I know that, as an architect, I’m very used to value managing my projects as I design.
I’m often told how surprised builders are that my designs are so ‘buildable’, whilst being functional, fantastic, family homes.
It’s largely because of the training ground I’ve had in my career, where my designs were constantly being assessed for their value. The value they had in lifestyle and liveability, in financial return, and in lowering construction costs.
I remember having a boss who used to drill into me: “Amelia, every line you draw is a material or product that has to be put into the back of a truck, brought to site, and carried by people or machinery, and put into place. How will that occur?”
Work with someone who is thinking about buildability whilst they design – but not limiting (or killing) the design outcome in the process.
Not every architect or designer has had similar career training to me. The fact that builders are so surprised at the buildability of my designs (and the many, many designs that I’ve seen myself) tells me this.
What else can you do?
Utilising readily available construction methodologies can also be helpful.
They’re well practiced by the many trades who use them, so that can make them faster.
Some are even pre-fabricated in factories so they can come to site partially made, and installed or erected very quickly. Time is money in construction, so saving time saves money as well.
Reviewing access on site can save time in set up, and save in having to move things around and rearrange things during the build.
In speaking to builders, it can be crazy how much time is spent stacking and restacking products on tight sites over the course of a project, so that one trade can complete their work … only to have those products moved around again for the next phase of work.
Bring forward your decision making, so that your team can work as methodically, proactively and efficiently as possible – and plan for the work ahead of time.
Every person who has to stand around on site waiting for a decision, or redoing something due to a change or unanticipated situation is money you can avoid spending with proper planning and preparation.
There’s lots of ways labour can be saved with the right design approach.
And having a builder and architect / designer working closely together, and getting their brains and experience into your project planning right from the start, can unlock huge savings for you.
This ideally happens DURING your design phase, so you create the right design approach to facilitate this type of build. It’s far more challenging to apply this after the design is done.
So where is your construction budget being spent in your renovation or new build?
Saving time during your build, and creating a less labour-intensive design may save you way more $$$ than a tile reselection ever will.
Create a balanced approach to identify potential savings in your project.
Remember – 50% materials, 50% labour.
And create the right team who can input their expertise when needed, to help you do this.
If you’d like to get started on your renovation or new build project, my Get Started Guide is a fantastic resource to help you do just that.
It will teach you the first steps any project needs to take, whatever your dreams, location or budget, and whoever you’re working with. Learn more about it here >>> GET STARTED GUIDE
And, if you’d especially like to get started on your home design, then the mini-course ‘Happy Home Design’ will help you.
You’ll learn more about what decisions really matter in happy home design, and how you can design a home that is functional, fantastic and feel-good >>> HAPPY HOME DESIGN
If you’d like to learn how to choose the right builder, and learn how the specific checks to do, and questions to ask, when interviewing builders for your project >>> CHOOSE YOUR BUILDER
Leave a Reply